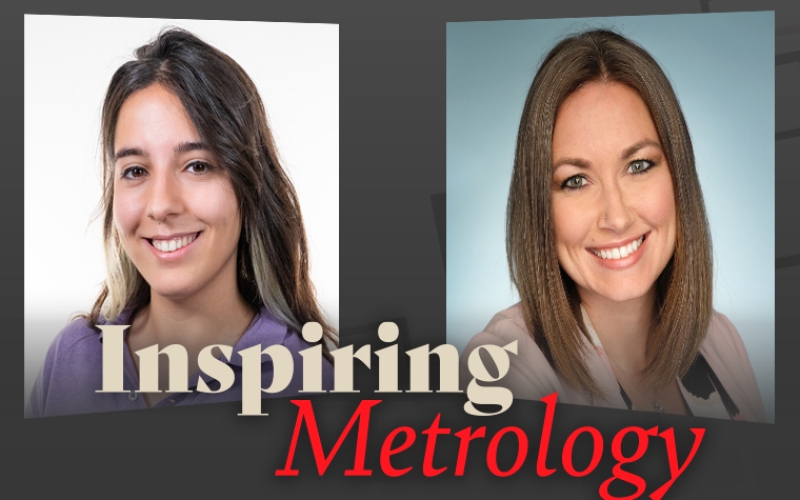
Inspiring Metrology: A conversation with Jackie Garofano
Inspiring Metrology: A conversation with Jackie Garofano, CTO at CCAT‘s
In a recent interview, Natalia Bermejo, Content Creator and Applications Specialist at Sensofar, had the opportunity to sit down with Jackie Garofano, the Chief Technology Officer (CTO) at the Connecticut Center for Advanced Technology (CCAT). During the engaging conversation, they discussed the transformative role of Sensofar’s optical profilers in the manufacturing ecosystem and cutting-edge technology’s impact on product quality and efficiency. Here are some highlights from the interview:
Jackie Garofano, Chief Technology Officer at CCAT, explained that CCAT‘s strategic partnership with us has been instrumental in achieving this goal. Sensofar’s optical profilers, specifically the S neox and S neox Five Axis systems, have been housed in CCAT‘s Advanced Technology Center, making them available to manufacturers, innovators, and researchers. The collaboration between CCAT and Sensofar has facilitated the adoption of high-accuracy 3D optical metrology in various industries, including aerospace, defense, and optics.
The accuracy and capabilities of Sensofar’s optical profilers make them a crucial tool in the manufacturing lifecycle, from design and testing to validation and supply chain management.
Over the years, metrology tools have seen significant advancements, particularly in emerging technologies like additive manufacturing and miniaturization. According to Jackie Garofano, Sensofar’s technology has evolved to meet the challenges of evaluating additively manufactured surfaces and fine features associated with miniaturization. Sensofar’s systems‘ user-friendly experience, automation capabilities, and fast data collection have played a vital role in supporting manufacturers’ need for accurate and non-destructive evaluation of surfaces.
Jackie Garofano emphasized that the unique value of working with Sensofar extends beyond cutting-edge technology. The people involved, including the US Sales Manager, Adam M. Platteis, and the global team, underpinned the collaboration.
Sensofar’s partnership with CCAT has allowed them to introduce companies in Connecticut to the suite of tools and highlight the availability of matching grants to subsidize technology onboarding. This access to trusted technology has created a win-win situation for both Sensofar and manufacturers, strengthening the relationship between the two.
Part 1/2
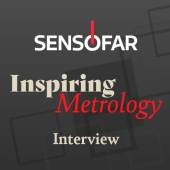
Part 2/2
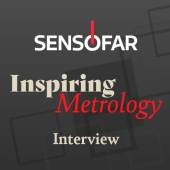
I am the Chief Technology Officer of CCAT, the Connecticut Center for Advanced Technology. We are based in East Hartford, Connecticut. So, along the northeast of the United States, we are an applied R&D center. So, our purpose is to really drive the adoption of leading-edge technologies into the manufacturing ecosystem. Particularly, CCAT is very focused on the small to medium-sized manufacturers that flow up to the larger OEMs that really move the global industry forward.
Interestingly enough, when I came into the role at CCAT, it was early 2021, and at the time, I had left nearly a decade-long career at what became Raytheon Technologies. I started out at the research center of what was then United Technologies and then moved into the corporate function to oversee an enterprise-wide leadership development program for engineering.
My time at RTX had come to a close, and the universe had a grander plan for me to be able to step into the role of leading technology here at CCAT, an organization that’s nearly 20 years old and with whom I’ve had an engagement with as a graduate student and also working as a research scientist at UTC. It was not ironic that microscopy is a very small world. So, your Regional US Sales Manager, whom I had worked with during my time at the research center, had reached out to me about introducing Sensofar to CCAT. And because of where we are based locally in the Connecticut region, it made a lot of sense for us to start discussing particularly a partnership of what that could mean between CCAT and Sensofar. And by partnership, really, it’s about having an opportunity to support the manufacturing ecosystem that the industrial base here in the state of Connecticut and then, of course, across the northeast.
So since then, since 2021, CCAT and Sensofar entered into what we call a strategic partnership, we have your technology housed within our Advanced Technology Center. We’re exposing it to manufacturers big and small, to innovators, to researchers. So, we have a diverse collection of individuals who walk through our doors. So it’s really been a fantastic partnership over the last couple of years.
It may be hard to believe, but I was. I’ve been doing research for nearly 20 years. I was fortunate enough as a freshman at university to start doing materials research, and at that time, it was really focused on high-resolution electron microscopy. So, through my time in graduate school, I was familiar with metrology, but as a hands-on experimentalist, I wasn’t actively doing that work. It wasn’t until I found my way into the industry after getting my Ph.D. that I learned about 3D Optical Profilometry, and certainly between then, which is ten years ago, and now, the ways in which the technology has advanced, and particularly with Sensofar being one of those technology providers that’s at that leading edge, then Sensofar provides the ability for anyone to really utilize their technology.
It is user-friendly, and it has great automation capabilities. It’s digitizing the data and really supporting anyone across industry verticals, whether you’re in industry or research and academia. It’s it’s quite a tool. So, I’ve been a fan for quite some time. Admittedly, I don’t do any work on the Sensofar machines that we have in-house, but my colleagues do speak very highly of it as well. We have been able to have other companies purchase Sensofar technology because they’re able to get their hands on it. Work with the team at Sensofar, who most often are co-located within our tech center. So it’s talking about a win-win. It’s certainly there, and we’re happy to be able to have Sensofar tech in-house.
I’m a former microscopist, and the research that I did was very much destructive. So having a good affinity for the capabilities of evaluating surfaces of, you know, very fine features in a non-contact, non-destructive way is critical. I didn’t have a real appreciation for the need until I heard about the industry. But graduate school is a different thing where you could really go down deep and have a different experience. Then, of course, the real-world applications across all the different industries. So Sensofar’s measurement systems enable people across all different industries to understand what is happening at this very fine feature, fine surfaces with great detail. And as we’re now in a very digitized way of manufacturing, it’s really important to have the user be able to do things quickly, to get data quickly, to get that accuracy. And in doing so, not disrupt where it is in the manufacturing process.
If you’re going through production or potentially what I’ve seen in my past life and industry is out when something is out in service, and you need to then analyze it for failure investigation, it’s really critical to have a tool or a suite of tools that enable you to do things. Not destructively.
I think I speak on behalf of the entire CCAT team. We’re working with Sensofar. It’s all about the people. Our mission at CCAT is to put people first. And truly, we want to be able to work with colleagues and partners across technology providers, across partners that we’re working with on federal or state or privately funded efforts. And really, it’s it’s the people. It’s your team.
Your international team allows us to not only have a foothold here in Connecticut and across the Northeast but also have a global organization to answer questions in the short term if we are experiencing any challenges. Has been extraordinary. So together, we are helping manufacturing companies have access to technology, demonstrate the value that Sensofar tools can bring to them, and then ultimately push that adoption into their manufacturing and into what they’re doing in their real life.
Many of the work that our customers are doing is proprietary. And so we do have news in place, which doesn’t allow us to really get deep into those more detailed success stories. However, I will say going back to the point of showcasing this technology to companies, having them see the value of investing in the technology they bring a problem to our tech center, sit at the Sensofar technology. Maybe a colleague from Sensofar partnered up with a CCAT engineer, or maybe they’re just a proficient user who can utilize the technology.
So there have been many success stories otherwise, right? People want to invest in the technology. And having that sustained success in a business is really critical. We have, you know, we here at CCAT, we serve the manufacturing ecosystem across various industries; although we are located in Aerospace Alley here in the Northeast, Aerospace and defense is pretty massive.
Other companies are working in space applications in optics and optoelectronics in, you know, thin films. So how Sensofar has demonstrated the ability for companies to adopt technology, have it be automated processes with fast and efficient data collection, has been critical.
The accuracy of 3D optical metrology systems, particularly for additive manufacturing or 3D printed surfaces, has certainly evolved. In my past life, I was looking at additively manufactured surfaces. And there were certainly challenges with the technologies that we were facing. I’m not saying that this was Sensofar right, because I’ve just been introduced to your company just two years ago. But it’s it’s certainly come a long way. And the ability for manufacturers to evaluate surface roughness, surface contours, non-planar surfaces, you know, especially with as we’re scaling down with miniaturization, having high accuracy of really fine features is paramount.
We have two S neox systems, one three-axis and the other the five-axis. So we’ve had this in-house for a couple of years now. Our technical team at CCAT really can’t say enough about the user experience of using the Sensofar tools. It’s, you know, especially when considering challenges many of us face with a skilled workforce.
You know, it’s great that technology providers are making it very user-friendly to collect data accurately, to have the automation, having the tools in place to scan extremely tiny orifices of sensitive chemical processing equipment additively manufactured surfaces that need to be within design tolerances critical.
And when you talk about, again, that miniaturization or moving into thin film assemblies, you know, having the ability to have a trusted technology is nothing more important than that. So, the UX of Sensofar technology is really getting a thumbs-up from our team here at CCAT.
I think having Sensofar in-house at CCAT Advanced Technology Center gives us a leg up because we’re able to have the US sales manager in-house quite frequently, as well as some of their colleagues on the Sensofar team here in the States, we’re able to introduce companies within Connecticut to the Sensofar suite of tools. And what’s great is that in Connecticut, we also have a Money for Manufacturing Matching Grants Program, which subsidizes the cost of onboarding technology, whether hardware or software systems. So Sensofar has been a wonderful partner because you all have, you know, gone out to market to tell companies that are in your portfolio here in Connecticut that there are these tens of thousands of dollars worth of matching grants available to them. So, that reduces the cost of the barrier.
The activation barrier of a company wanting to onboard this technology. They could sit our in our microscopy area. They could speak to your colleagues, they could partner up and work with CCAT on, you know, demonstrating the technology for their purpose. So it’s been a win-win as well, having Sensofar as a global company.
So model-based systems engineering, model-based design, model-based definition, anything that’s model-based of digitizing either a product or parts to create a digital twin. So then taking it through that manufacturing lifecycle, from design to manufacturing, test validation through supply chain… Having that digitized piece of technical data is so critical.
We’re seeing that all across the country, global companies, the Department of Defense, and many other agencies are now requiring us to become much more digitized using systems engineering in a way in which it’s enabled by or activated by model-based workflows. So, with the ability to effectively create a very high-resolution digital twin of the surface of whatever part you’re trying to manufacture, Sensofar technology supports the ability to get as much data as possible. Known data of the part from the effective feedstock. And then you take that through through your manufacturing process, whether it’s additive manufacturing, subtractive, forging, you know, you’re testing it. It contributes to that grander picture of model-based workflows and model-based systems engineering.