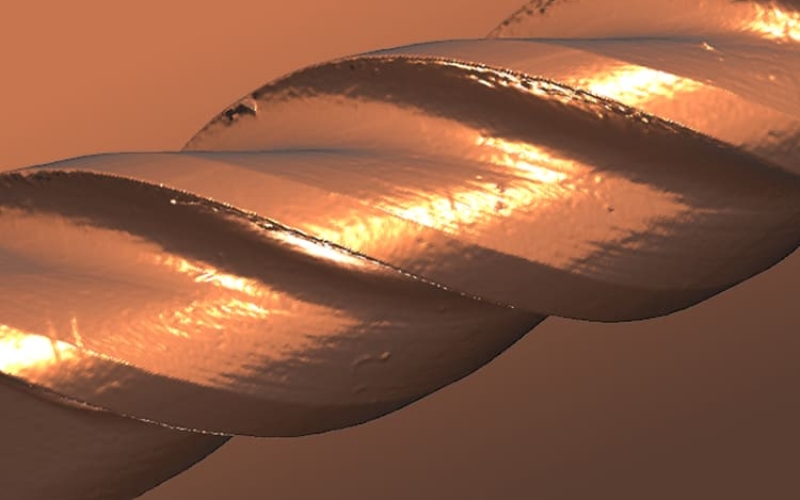
Multi-perspective characterization of an end mill
Natalia joined Sensofar shortly after finishing her bachelor’s degree in Nanoscience and Nanotechnology at Universitat Autònoma de Barcelona (UAB) 2018. Since then, she has provided technical and application support for the Sales team and the training and installation of systems for prospective clients and customers. In 2020, Natalia moved to Silicon Valley for a year to provide metrological support to high-tech companies. Following her previous role, Natalia transitioned to content generation within the Marketing department. Since then, she has occupied a hybrid position bridging sales and marketing, where each function mutually enhances the other.
In the tooling industry, optical metrology is crucial in achieving success from both design and tool use perspectives. Optical profilometers provide valuable information to help manufacturers optimize their tools and processes.”
One of the critical applications of optical metrology in tooling is the dimensional characterization of cutting tools to ensure that tools perform optimally and have a long service life. In addition to dimensional characterization, roughness measurements can be interesting for predicting how well the removed material will exit the tool. This information is critical in preventing clot formation or overheating of the tool during use.
Optical metrology systems can also provide local measurements to help identify potential cutting tool issues. For example, these systems can detect chipping or coating peeling, indicating that a tool needs to be replaced or repaired.
It is important to note that these characterizations can come in very different orders of magnitude. Dimensional measurements of common end mills, for example, are typically within the millimeter range, while chipping or roughness assessments generally are on the micron scale. Yet, it is nowadays possible only with one set-up: a Sensofar system, the S neox Five Axis, with Digital Surf software, SensoMAP.
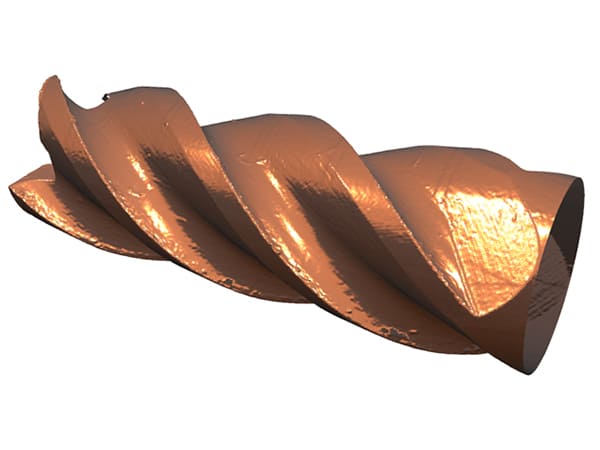
3D SHAPE ACQUISITION
Optical metrology systems like Sensofar’s S neox Five Axis are critical in characterizing various parts and optimizing manufacturing processes in the tooling industry. The S neox Five Axis system can acquire the entire 3D shape of objects, including end mills, and offers high precision and accuracy.
One of the key features of the S neox Five Axis system is its rotational module, which allows for the complete measurement of a sample’s shape. This feature is particularly useful in the tooling industry, where precise measurements of cutting tool geometries are critical to achieving optimal performance.
After acquiring the necessary data, we analyzed the mesh data comprehensively. This is where the SensoMAP software proves extremely useful, particularly its Shell Module, which allows for extracting information from mesh data at various levels.
The Shell Module of SensoMAP software is a powerful tool that enables users to extract dimensional and roughness information by navigating from mesh to topographical data and then profile data. This module provides an effective means of obtaining valuable insights from the acquired data.
DIMENSIONAL ANALYSIS
In our analysis, we performed several measurements using parametric profiles generated from shell data to understand the endmill’s geometry comprehensively.
The first measurement involved extracting cross-section measurements perpendicular to the cutting axis of the endmill at multiple locations along the flute length (as shown in Figure 2). By doing so, we could determine whether the tool maintained a consistent external diameter across its entire length. Additionally, we calculated the concentricity between the inner and outer circles to check for any tool run-out.
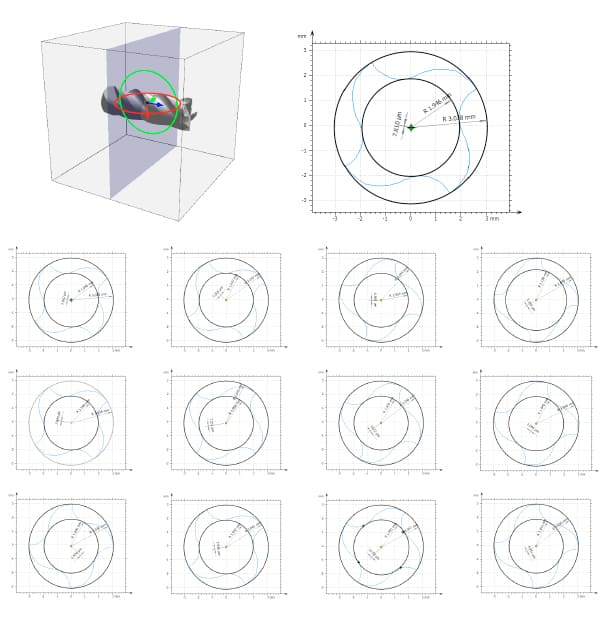
The second measurement aimed to examine the pitch of the helix. To achieve this, we fitted the tool into a cylinder and unrolled it. Next, we extracted a profile perpendicular to the helix angle and measured the pitch distance (Figure 3). This measurement provided valuable insights into the endmill’s geometry and was crucial in ensuring it functions optimally.
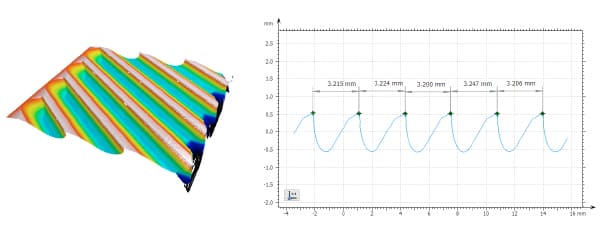
ROUGHNESS ANALYSIS
The surface finish of the edges plays a crucial role in determining the outcome. Therefore, we utilized the previously unrolled data to take a profile on top of the flute and calculated the roughness parameters according to ISO 4278.
By doing so, we ensured that the end part would have clean edges rather than rough ones, which can negatively impact the quality and performance of the final product./vc_column_text]
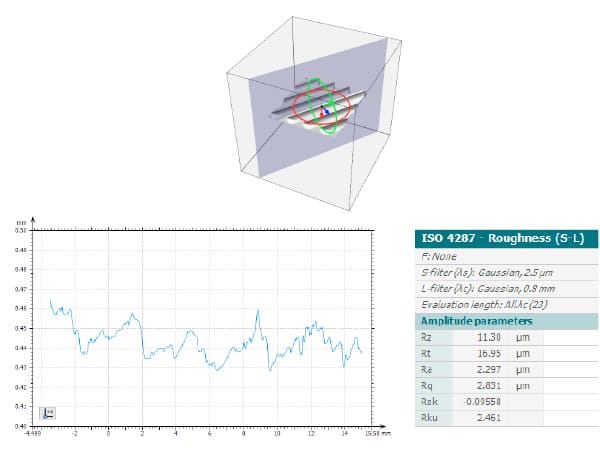
PEELING ASSESSMENT ON A CUTTING TOOL
One of the most promising features of cutting tools is their coating, which significantly impacts their durability and ability to withstand high-stress processes. Coated cutting tools have been shown to last longer and perform better than their uncoated counterparts. However, coating peeling is a significant concern and can significantly impact the performance and durability of the tool.
Fortunately, the Shell Module from SensoMAP offers an excellent solution to this issue by enabling the extraction of topographies from the mesh (Figure 4).
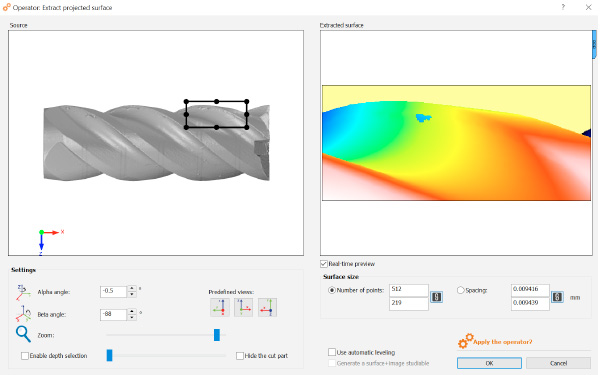
By utilizing particle analysis, we can focus solely on the areas where peeling has occurred and determine the extent of the damage. This allows us to understand the peeling area’s dimensions and decide whether it is limited to the coating or if some material is missing due to chipping.
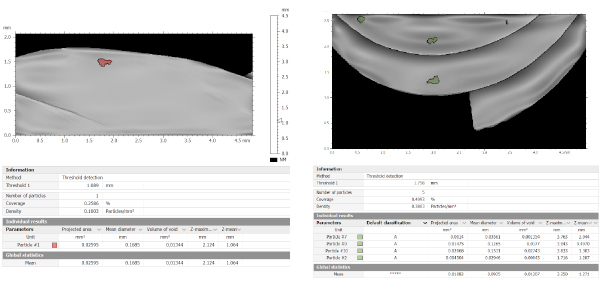
By identifying the extent of coating peeling and chipping, we can take appropriate action to ensure that the tool remains in optimal condition and performs to its fullest potential.
Integrating the S neox Five Axis and SensoMAP has proven to be an exceptional solution for tooling applications. The S neox Five Axis’s innovative combination of three different measuring technologies and a rotational module has made it an indispensable tool in the tooling characterization process. Additionally, SensoMAP provides a comprehensive suite of analysis tools for shells.
This combination of SensoMAP and S neox Five Axis made it possible to characterize an end mill’s dimensions, roughness, and peeling defects. With this innovative technology, manufacturers can achieve unprecedented levels of precision and accuracy, making it possible to produce high-quality products that meet the demands of today’s market.