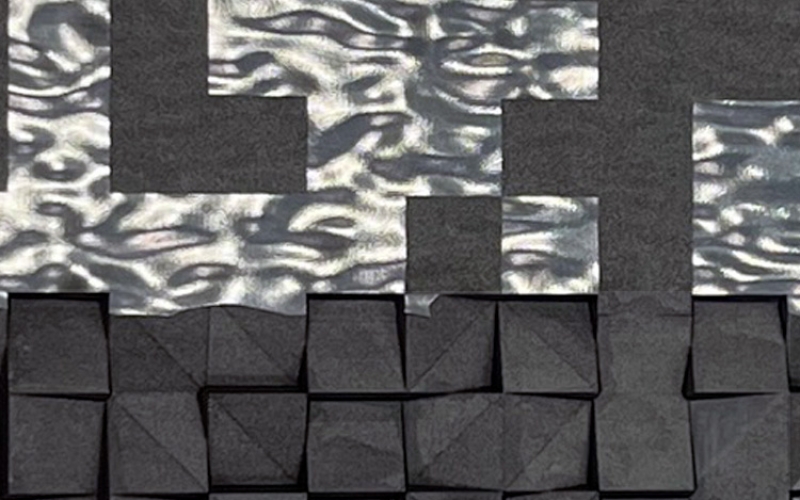
Laser engraved steel insert dimensional analysis
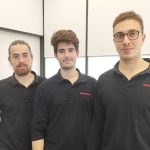
Quim Jané, Nil Ruiz and Raül López
Established in 1983, Microrelleus SL specializes in functional and design laser texturing services, laser micro-milling, and industrial engraving for molds, tools, and pieces. In 2016, Microrelleus was the first to use a femtosecond laser machine in five axes to meet its customers’ needs. They also use nanosecond lasers for machining in five axes, milling machines, and die-sinking EDM.
With Sensofar S wide we were able to measure all the geometry in a single take and could verify that everything was within the required parameters.
Laser technology is perfectly suited for manufacturing micro-cavities in molds, microfluidic channels, or even micro-milling for tempered steel or hard metal tools. We use nanosecond and femtosecond lasers to achieve excellent surface quality. For this reason, laser technology is used for functional texturing, where the nanostructures engraved add functionality. For example, we can create structures that reduce friction or increase diffraction, trapping, or diffusion. Other structures could be super hydrophobic or even antibacterial.
For functional texturing, ultra-short pulse duration lasers, like femtosecond lasers, have two main advantages. Firstly, the micro-milling is burr-free, and so there is virtually no thermal effect on the part. The result is a clean, sharp micro-milling with defined edges and high-quality surface finishing. Secondly, because it is a “cold laser,” we can engrave over any material: sapphire, plastic, glass, ceramic, aluminum, steel, etc.
In other words, using femtosecond lasers, we can engrave directly over parts made from materials such as plastic and transparent glass with total homogeneity.
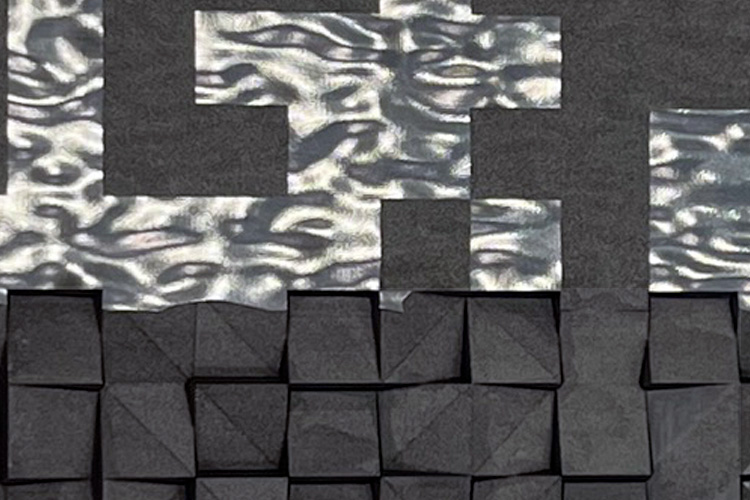
Study of a diffusing texture
The sample we want to study is a steel insert engraved using a Femtosecond laser (Figure 1). The part consists of two different geometries: The first is made by flat surfaces intersecting. The other geometry is a wavy surface with small details. Both geometries have a diffusing texture on their surface.
Both structures are made to create a specific effect when the light goes through the injected plastic part, and with the diffusing design, we want to create a homogeneous light distribution. This part aims to inject PMMA and then do a photometric study. With Sensofar’s results, we can know the parameters to adjust the optical simulator with precision.
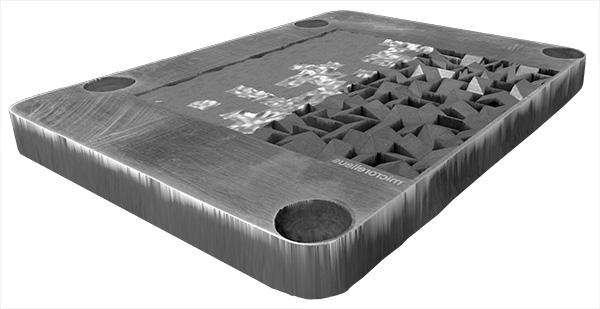
We measured with the S wide system to characterize this part. It uses Fringe Projection technology, which measures a surface by detecting the change of pattern on the structured light projected. This technology allows measuring large areas with sub-micron repeatability. Thanks to the Fringe Projection system and automatic stitching, we measured everything at the highest quality possible in just a few minutes (Figure 2).
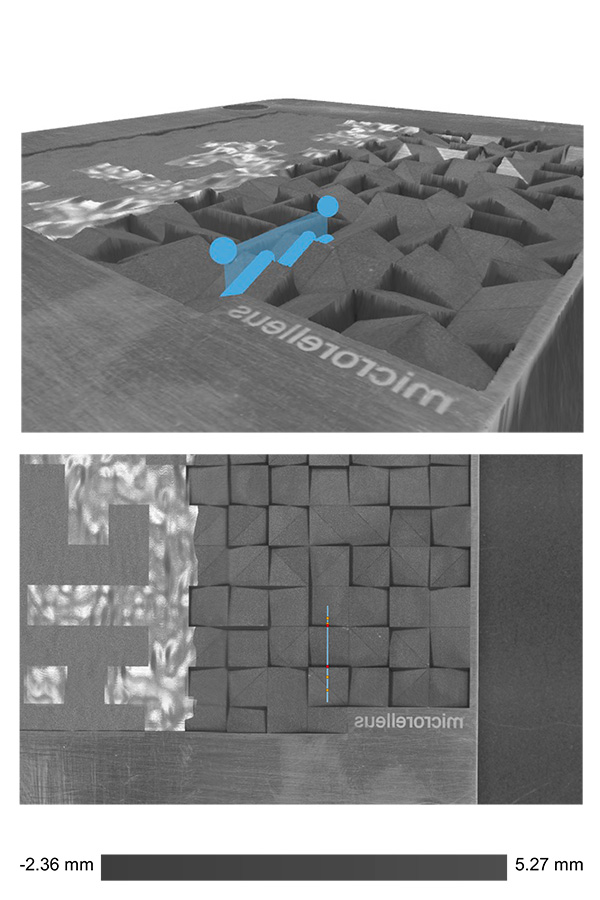
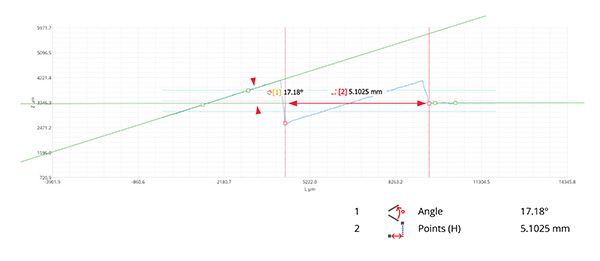
Knowing the engraving results (shape, angles, surface quality) is essential to ensure everything is within the optical requirements. With Sensofar S wide, we can measure all the geometry in a single take, verifying that everything was within the required parameters (Figure 3).
Sensofar’s Fringe Projection technology is effective in analyzing functional texturing on the micro-scale. As a result, we can obtain fast and non-destructive measurements to ensure that functional texturing will work adequately.
Thanks to the S wide, we can offer excellent quality control adding, with SensoVIEW, all the details about the geometry summarized in a report. The S wide also beats some typical limitations of Fringe Projection systems since we can measure polished surfaces.