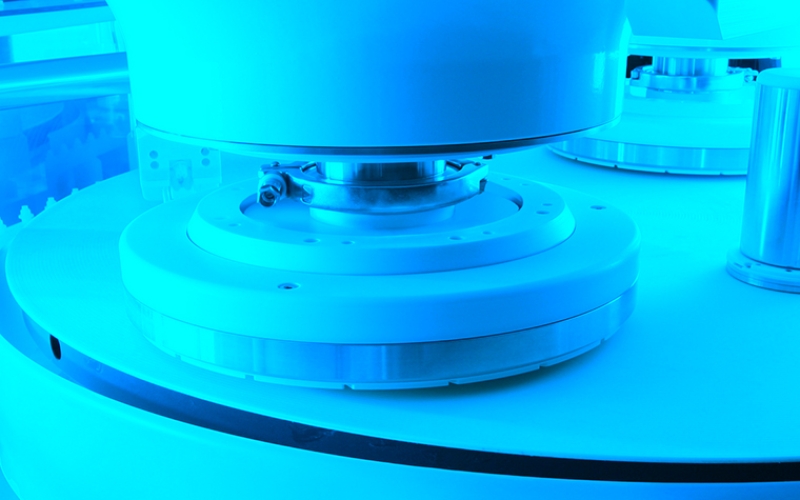
In-situ metrology for pad surface monitoring in CMP
David studied his bachelor’s degree at the Polytechnic University of Catalonia (UPC), where he started to work as a Research Assistant in the Department of Physics. Once he finished his master’s degree at the University of Barcelona (UB) he entered into the world of optical metrology joining Sensofar. As a Sales Specialist, he communicates Sensofar’s knowledge about optical metrology and trains our customers on how to extract the full potential of our systems. If you need him, he’ll probably be in our demo room measuring samples or performing live demonstrations.
Thanks to S mart 2 it has been clearly demonstrated that CMP pads are largely under-utilized and are often discarded with more than half of the useful lifetime still remaining.
Chemical Mechanical Planarization (CMP) is a critical process in the semiconductor, hard disk, and LED wafer manufacturing industry used to achieve the required planarity of the substrate wafer. Planarization is crucial for ensuring the functionality of the multi-level interconnects within the structures and reducing wafer thickness while maintaining uniformity.
CMP is expected to play an increasingly important role in the future development of microelectronic devices as the feature sizes continue to shrink and the integration levels continue to increase. By precisely controlling the surface topography and material properties, CMP can enable novel device architectures, such as 3D stacking, finFETs, nanowires, and quantum dots. In addition, Chemical Mechanical Planarization can also facilitate the integration of new materials, such as high-k dielectrics, low-k dielectrics, copper, cobalt, graphene, and carbon nanotubes, by overcoming the limitations of conventional etching techniques.
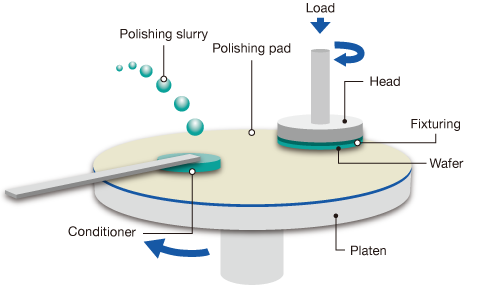
How does CMP work?
CMP combines chemical and mechanical forces to remove excess material and create a smooth, flat surface on a semiconductor wafer. It is a vital technique for achieving high-quality and high-performance microelectronic devices. CMP is widely used in the industry for various applications, such as :
- Planarizing interlayer dielectrics (ILDs) and metal layers in integrated circuits (ICs) to reduce parasitic capacitance, improve reliability, and enable multilevel interconnects.
- Planarizing shallow trench isolation (STI) structures to isolate active devices and prevent leakage currents.
- Planarizing silicon-on-insulator (SOI) substrates enhances device performance and reduces power consumption.
- Planarizing microelectromechanical systems (MEMS) to improve functionality and integration with ICs.
- Planarizing magnetic disks and read/write heads for computer hard drives to increase storage density and data transfer rate.
During the CMP process, the wafer is held on a rotating fixture and pressed against a rotating polishing pad. At the same time, an abrasive chemical liquid (called slurry) is distributed between the wafer and the pad. The chemical slurry weakens the wafer’s surface, allowing material removal by the asperities of the pad. This process is repeated until the desired level of planarity is achieved.
CMP is a complex and challenging process that involves many parameters, such as slurry composition, pad material, pressure, velocity, temperature, and endpoint detection. In particular, the surface properties of the polishing pad play a significant role in the quality of the CMP process, as they can affect the quantity of material removed from the wafer. As the polishing pad degrades during the polishing process, it needs to be constantly reconditioned. This is typically done through an abrasive process on the pad surface, using a rotating abrasive or conditioning disk made of stainless steel or electroplated diamond.

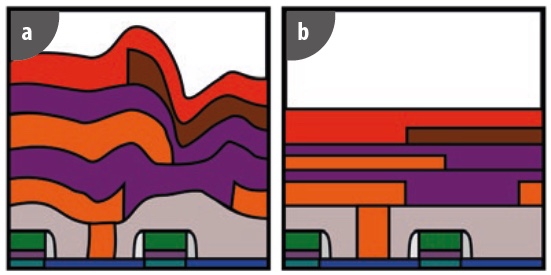
Surface metrology for CMP
Surface metrology is key in the Chemical Mechanical Planarization (CMP) process, as the mechanical interaction between surfaces is a significant variable for all process stages. The surfaces that require periodic characterization throughout the CMP process include the conditioning disk surface, the wafer surface, and the pad surface.
In high-volume production environments, it’s very important to have non-destructive in-situ pad characterization during natural pauses in the polishing process, such as when changing wafers. This enables the detection of drifts in key pad parameters and assists in validating process changes. Ultimately, the goal is to extend the lifetime of consumables and improve the yield of the entire process, which is essential for any successful manufacturing operation.
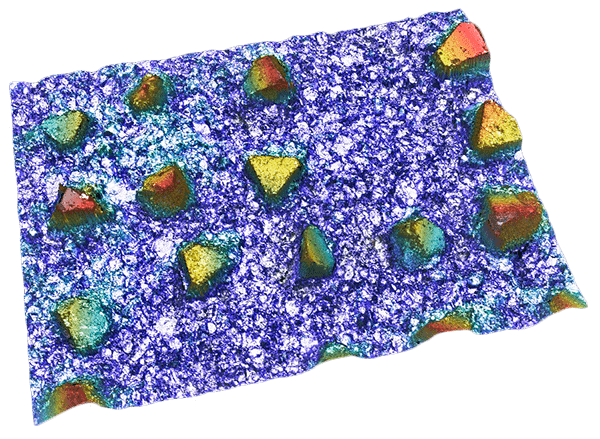
Two main factors affect pad surface degradation and lifecycle – pad groove occlusion and pad glazing.
Groove Occlusion
During polishing, the material removed from the wafer deposits in the pad grooves, causing occlusion. This phenomenon prevents uniform slurry distribution across the wafer, leading to non-uniform removal between the center and edge of the wafer.
To predict the need to clean the pad grooves and determine the best time for it, groove occlusion monitoring is necessary. Cleaning operations can extend pad lifetime by up to 20% .
Pad Glazing
Pad glazing is a more complex phenomenon that occurs when the polishing ability of the pad is reduced due to surface degradation. This phenomenon enhances wear between the wafer and pad, increasing process temperature and producing material selectivity during polishing.
Unlike groove occlusion, pad glazing cannot be predicted easily and requires constant monitoring to ensure the ideal performance of the CMP process.
In-situ pad surface monitoring is essential for both groove occlusion and pad glazing. For this purpose, the metrology approach used must be able to work under wet conditions. Immersion metrology is the only approach that can meet these requirements.
The main benefit of this approach is that the pad does not need to be removed from the polisher for characterization. This makes it possible to monitor pad glazing and groove occlusion in situ at various points in the pad’s life cycle. In-situ metrology has been shown to extend pad lifetime, allowing operators to utilize the pads until the end of their useful life.
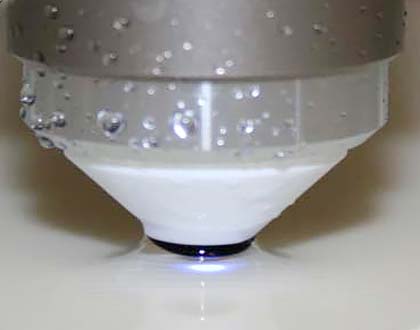
In-situ immersion metrology system
Sensofar collaborated with industry experts to develop an innovative surface metrology solution for the CMP process several years ago. The aim was to increase yield per pad and minimize downtime of polishing systems by allowing pad changes only when necessary. The solution was the non-destructive, in-situ 3-in-1 surface metrology system called S mart 2.
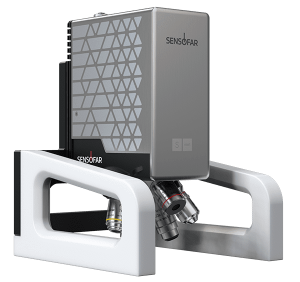
With S mart 2, you can quickly assess the status of polishing pads using a portable stand and place the sensor on the pad while it’s still inside the polishing system. The new head is designed to be lighter and more compact. It has an embedded electronic controller that makes it a plug-and-play system requiring only two cables (power and communication) exiting the head.
The S mart 2 system can be directly operated from a laptop, improving portability and convenience. It can also be used as a standalone system or integrated into a production line as an automatic metrology solution. With S mart 2 you can rapidly acquire and analyze data to effectively monitor crucial pad characteristics such as glazing and groove occlusion.
The previous version of S mart already proved that CMP pads were under-utilized and often discarded, with more than half of their lifetime remaining. With the introduction of S mart 2, it is even easier to monitor pad conditions and prolong their lifespan successfully.
S mart 2 for CMP monitoring
S mart 2 is provided with Sensofar patented technology and a high-intensity blue LED, combining Confocal, Ai Focus Variation, and Interferometry technologies within a single sensor [3]. The SensoPRO software plugin built around the CMP application provides all the necessary tools and analysis for this application within the S mart 2 control interface.
The S mart 2 sensor offers a unique metrology approach that, when paired with an appropriate immersion objective, enables accurate measurement of pad asperities even while still on the polisher.
- Monitoring groove occlusion
By utilizing Confocal and Ai Focus Variation technologies, groove depth and width can be swiftly detected and monitored, allowing for efficient identification and tracking of groove occlusion. For production environments, automatic analysis is possible through a SensoPRO software plugin that independently determines the groove’s width and depth, regardless of its orientation.
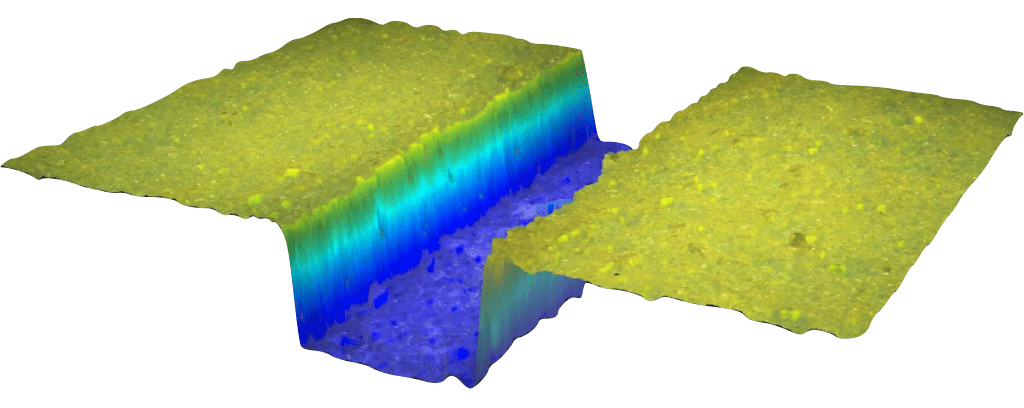
- Pad glazing monitoring
Smart 2 and its Confocal technique compatible with water immersion conditions can effectively characterize pad asperity after conditioning and polishing phases. Monitoring the pad’s condition can determine the best time for conditioning and the optimal duration needed to regenerate the pad surface. These capabilities help prolong the pad’s usable lifespan, minimize the need for control wafers, and optimize the overall process, preventing the need for re-processing of finished wafers.
This image displays how the pad’s asperity height changes during polishing. As polishing continues for several hours, a ‘glazing peak’ can be observed in the surface distribution. Monitoring the pad surface at intervals throughout the process makes it possible to intervene and condition the pad surface to revert it back to its initial state. Use this information to optimize your polishing process and achieve consistent results.
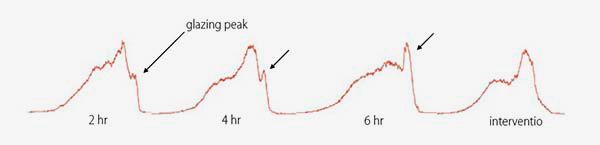
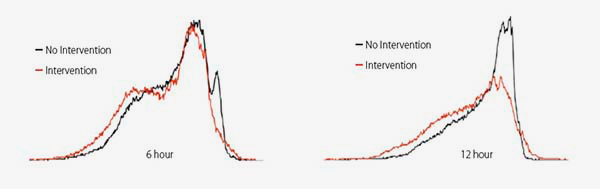
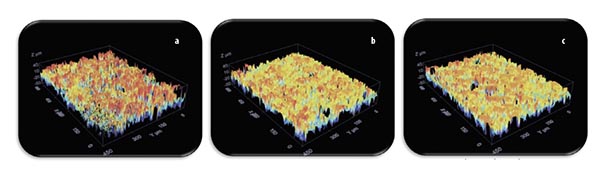
- Automatic analysis
The S mart 2 sensor makes precise control of surface parameters easy. The analysis of acquired data can be automated, allowing operators to place the sensor over the pad surface, acquire the measurements and obtain a report. Sensofar’s SensoPRO software automatically displays the target parameter value and the pass/ fail report for the specific tolerance, streamlining the process and reducing the likelihood of errors.
SensoPRO is a powerful tool for quality control managers, enabling direct comparison between sets of data and the establishment of automatic tolerances for CMP monitoring. With SensoPRO, you can quickly and easily analyze and compare data, ensuring consistent quality and process control.
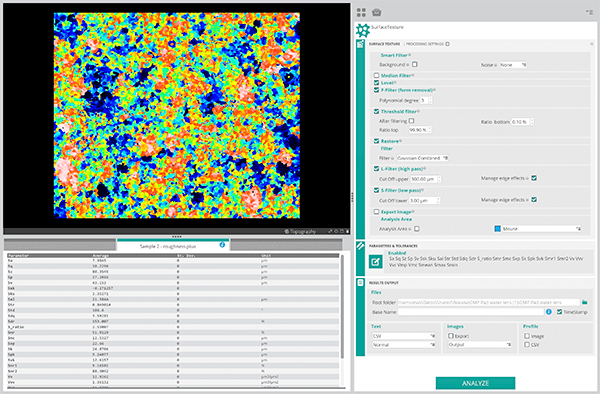
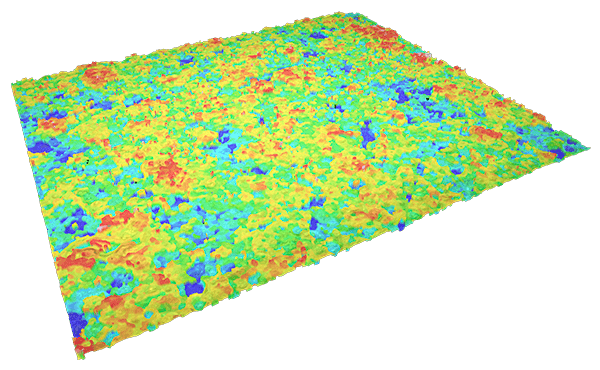
Conclusions
CMP ensures the planarity and functionality of structures built on a wafer. With advancing technology, CMP is becoming even more important, making it a critical area of focus for researchers and manufacturers. In this context, in situ surface measurement is essential for monitoring the CMP process, reducing costs, and ensuring quality. Sensofar’s new S mart 2 provides advanced acquisition and analysis tools to support CMP research and quality control. By leveraging the advanced capabilities of S mart 2, researchers and manufacturers can optimize their CMP processes, achieve superior results, and stay ahead in a rapidly evolving industry.
References
- Mahadevaiyer Krishnan, Jakub W. Nalaskowsk, and Lee M. Cook, “Chemical Mechanical Planarization: Slurry Chemistry, Materials, and Mechanisms” Chem. Rev., 2010, vol. 110, pp 178–204.
- Zhengfeng, Wang, Yin Ling, Ng Sum Huan and Teo Phaik Luan. “Chemical Mechanical Planarization.” (2001).
- J. McGrath, C. Davis. Polishing pad surface characterization in chemical mechanical planarization. Journal of material processing technology, 153-154 (2014).
- T. Moore, N. Schwarz. NEOX Ex-Situ CMP Pad. NCCAVS, CMP Users Group Proceedings (2013).
- R. Artigas, F. Laguarta, C. Cadevall. Dual-technology optical sensor head for 3D surface shape measurements on the micro- and nanoscale. Optical Metrology in Production Engineering, Proc. SPIE 5457 (2004).